Clamping jaws have a great influence on the clamping quality and safety and thus also on the machining results.
Jaws typically are available in the following versions:
- Hard, Steel
- Soft, Aluminum
- Serrated
- Dovetail
- Inserted
- Pivoting or Pendulum
- Pin-Type
Top Jaws
Top Jaws mount to the top of the Jaw carrier and provide maximum vise capacity. Modification of a vise to hold workpieces from the top of the jaw carrier, when not provided with a factory provision for Top Jaws, is strongly discouraged.
Floating Jaws literally freely float between workpieces between the vise jaws. If the workpieces are of a repeatable predictable size, prior to machining, floating jaws are a great way to improve part density and throughput when using a vise. (image from CLR)
Virtually every Vise manufacturer has at least one Quick-Change Jaw solution. The challenge with these solutions becomes scalability. Manufacturers, from time-to-time change and evolve their designs, obsoleting prior jaw connection systems. For companies with hundreds of special jaw sets this can present a significant issue in both costs, to buy a new system and jaws, and time, the necessary machine capacity to machine the jaws. The time, effort, and acquisition of these solutions are frequently revealed driveled by the cost of a dedicated fixture.
Clamping Claws are designed to firmly attach the vise to a T-Slotted Machine Table. Typically, they are specific to each vise model and can be used with a T-Nut or in a plain threaded hole. They do not provide any precision alignment of the vise to the machine.
Vises, with only two jaws, do not constrain the workpiece in all 5-degrees of freedom. In order to prevent the misloading of a workpiece and Workpiece Stop of some kind must be used to ensure the proper workpiece position. Various types are commonly available.
Right-Angle Drive
Most manual machine vises use a crank handle that is this parallel to the base of the vise and thus the machine table. This can create an issue where the handle may be restricted from certain movements by the table. When oriented vertically, especially in horizontal machining centers, a different issue is created as the operator must reach above the top of the tooling block to turn the handle. The Right-Angle Drive allows the use of a handle crank but orients the handle perpendicular to the base of the vise.
Quick-Change Vise Systems
Quick-Change Jaws Virtually every Vise manufacturer has at least one Quick-Change Jaw solution. The challenge with these solutions becomes scalability. Manufacturers, from time-to-time change and evolve their designs, obsoleting prior jaw connection systems. For companies with hundreds of special jaw sets this can present a significant issue in both cost, to buy a new system and jaws, and time, the necessary machine capacity to machine the jaws. The time, effort, and acquisition of these solutions is frequently rivalled by the cost of a dedicated fixture.Many Quick-Change Vise Systems, like those commonly available for 5-Axis Vises, are usually mechanical or Power-operated Zero-Point Systems. These systems use pins, affixed to the bed of the vise, to provide both clamping and locating. Repeatability varies between systems. Learn more about Zero point here.
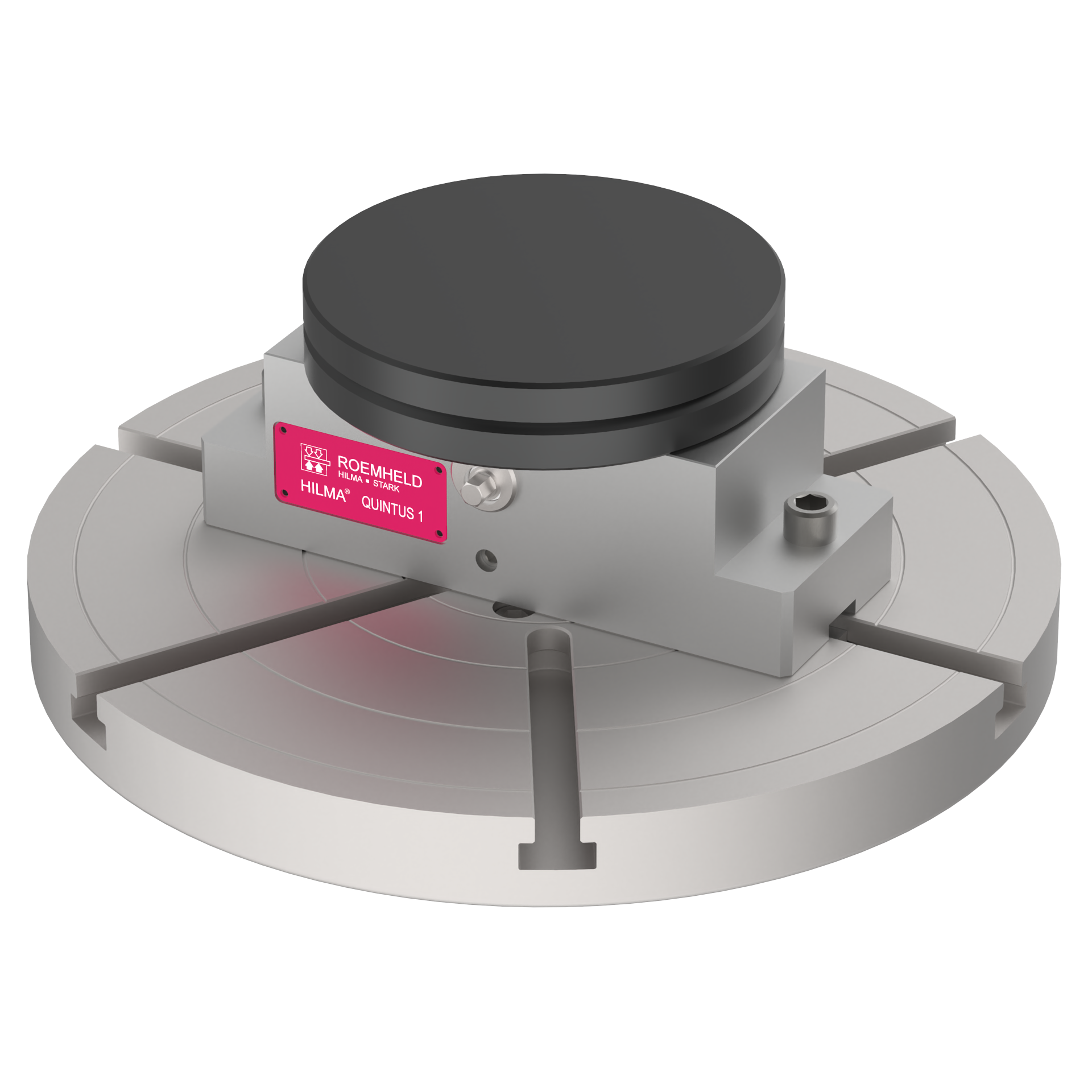